-
Startup Marketing Strategy: 18 Ideas and Tactics That Actually Work
Stop copying enterprise playbooks — use these startup-friendly marketing strategies to dri...
Bob Dearsley
3/13/25
-
The 12 Best Free Flowchart Templates [+ Examples]
From sales to onboarding, these free flowchart templates help you visualize workflows, opt...
Aimee del Principe
3/13/25
-
Top Marketing Channels in 2025 — Here’s What Your Team Needs to Master [Data]
Marketing in 2025 is all about AI, video, and authenticity. See which channels are deliver...
Clifford Chi
3/12/25
-
How AI Will Revolutionize the Future of Business, According to HubSpot's CMO
Here’s how AI has already disrupted business and what to expect as the AI revolution conti...
Kipp Bodnar
3/12/25
From HubSpot's video library
-
How to Start Affiliate Marketing With No Experience or Money (4 Free Tools!)
-
How Airlines Really Make Money | Hustlenomics | The Hustle
-
What Entrepreneurs Can Learn From Native Deodorant
-
Meet the Designer Behind the Iconic Nudie Suit | Unknown Empires
-
Tips For Elevating Your Next Go-To-Market Strategy (+ Free Templates)
-
Why T-Mobile Trademarked This Color | The Hustle
-
How to Start Affiliate Marketing With No Experience or Money (4 Free Tools!)
-
How Airlines Really Make Money | Hustlenomics | The Hustle
-
What Entrepreneurs Can Learn From Native Deodorant
-
Meet the Designer Behind the Iconic Nudie Suit | Unknown Empires
-
Tips For Elevating Your Next Go-To-Market Strategy (+ Free Templates)
-
Why T-Mobile Trademarked This Color | The Hustle
-
How to Start Affiliate Marketing With No Experience or Money (4 Free Tools!)
-
How Airlines Really Make Money | Hustlenomics | The Hustle
-
What Entrepreneurs Can Learn From Native Deodorant
-
Meet the Designer Behind the Iconic Nudie Suit | Unknown Empires
-
Tips For Elevating Your Next Go-To-Market Strategy (+ Free Templates)
-
Why T-Mobile Trademarked This Color | The Hustle
-
AI Intent — Figuring Out the Purpose that Drives Service Tech
AI intent is an AI system’s ability to understand the meaning behind a user’s input. Disco...
Kolawole Samuel Adebayo
2/21/25
-
Level Up Your POS Experience — Here's What Experts Have to Say
The POS experience is an important transactional moment for your customers. Here's why — a...
Nakul Kadaba
2/21/25
-
Training AI Chatbots — The Guide for Service Teams
Uncover the insights that will help you train AI chatbots effectively, ensuring they deliv...
Kolawole Samuel Adebayo
2/19/25
-
Top 12 Free Help Desk Software & Ticketing Systems
If you're ready to take customer experience to the next level, you'll need help desk and t...
Rami El-Abidin
2/18/25
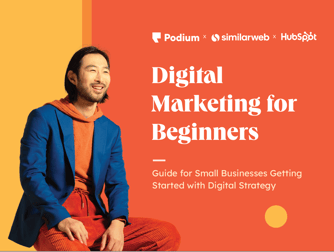
An Introduction to Digital Marketing
Learn the basics of digital marketing and explore different ways to reach your ideal customer.
-
5 Bad Sales Behaviors Holding You Back — According to the Pros
You might be sabotaging your sales without even knowing it. See five bad sales behaviors y...
Dagny Dukach
3/13/25
-
5 Reasons Why Sales Teams Miss Revenue Targets [+ How to Meet Them]
Why are revenue targets so hard to hit? To shed some light on the matter, I’ll offer my pe...
John Holland
3/13/25
-
I Explain Financial Forecasting Models & Methods Using Layman’s Terms
Explore popular models and methods for financial forecasting, plus discover the best finan...
Osama Zahid
3/12/25
-
What I’ve Learned About Selling Online Courses (and How You Can Too) [+ Expert I...
Learn everything you need to know about successfully selling an online course, from course...
Taylor Cromwell
3/12/25
From the HubSpot Podcast Network
-
Business Made Simple
Your Website Probably Stinks—Here’s How to Fix It!
-
The Science of Scaling
How to Scale a Billion Dollar Sales Team w/ John McMahon (Board Member, Snowflake)
-
Truth, Lies and Workplace Culture
From Bystander to Ally: How to Avoid DEIB Washing
-
Imperfect Action
The art of the post-launch review: 5 questions to make your next launch a success
-
Latinx In Power
Harnessing the Power of Silence in Negotiation with Diana Kleps
-
The Sales Evangelist
5 Ways To Do Daily Outbound With LinkedIn
-
Business Made Simple
Your Website Probably Stinks—Here’s How to Fix It!
-
The Science of Scaling
How to Scale a Billion Dollar Sales Team w/ John McMahon (Board Member, Snowflake)
-
Truth, Lies and Workplace Culture
From Bystander to Ally: How to Avoid DEIB Washing
-
Imperfect Action
The art of the post-launch review: 5 questions to make your next launch a success
-
Latinx In Power
Harnessing the Power of Silence in Negotiation with Diana Kleps
-
The Sales Evangelist
5 Ways To Do Daily Outbound With LinkedIn
-
Business Made Simple
Your Website Probably Stinks—Here’s How to Fix It!
-
The Science of Scaling
How to Scale a Billion Dollar Sales Team w/ John McMahon (Board Member, Snowflake)
-
Truth, Lies and Workplace Culture
From Bystander to Ally: How to Avoid DEIB Washing
-
Imperfect Action
The art of the post-launch review: 5 questions to make your next launch a success
-
Latinx In Power
Harnessing the Power of Silence in Negotiation with Diana Kleps
-
The Sales Evangelist
5 Ways To Do Daily Outbound With LinkedIn
-
Website Quality Assurance: How I QA My Website for Maximum Impact
Learn the importance of website quality assurance, with tips and expert insights to ensure...
Darrielle Evans
3/13/25
-
Creating a Web Design Contract That Keeps Your Project on Track [+ Expert Tips]
Learn from experts how to create a web design contract that protects your business, sets c...
Jenny Bergen Clark
3/13/25
-
HTML Form Templates [50+ Best Examples]
These are the 50+ best HTML Form templates for login forms, signup forms, contact forms, s...
Madhu Murali
3/13/25
-
Drag-and-Drop HTML Editor: Elevate Your Site With My Favorite Builders
Learn how the best drag-and-drop website builder can help your content strategy. Then, exp...
Alex Girard
3/13/25
-
A/B Testing Your Website — All The Tips Devs and Marketers Need to Know
Learn about A/B testing websites, including why it matters, how to do it, and what to meas...
Nathan Ojaokomo
3/12/25
-
15 Stunning HTML Websites [+ How They Work]
Discover stunning HTML websites and learn how to build your own. Then, explore HTML websit...
Colin Newcomer
3/11/25
Explore more topics
Ready to brush up on something new? We've got more to read right this way.